Sanborn Embossing Press, American
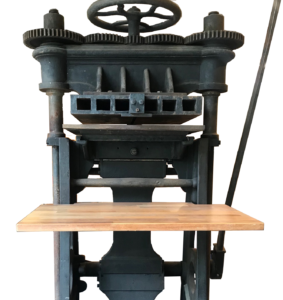
An imposing 7 feet tall, the Sanborn embossing press greets visitors at the entrance to the Museum.
In 1884, Geo. H. Sanborn & Sons published a catalog of its bindery equipment, which included its No. 5 Embossing Press, described as a longtime favorite in the industry and recommended for general work. Embossing presses like the No. 5 had been standard equipment in binderies since the 1830s because they produced enough heat and pressure to work with the cloth-covered board cases, and eliminated the handwork once required when covers were custom made for each book.
These presses made it possible to cover cases with cloth and decorate them inexpensively in one step, making a major contribution to the mechanizing that took over book production. They also made it possible to quickly and cheaply produce edition bindings, which were large quantities of the same book turned out in uniform cases.
By the end of the nineteenth century an ever-growing reading public could afford moderately-priced mass-produced books. But these readers, publishers soon realized, wanted more than books they could afford. They wanted the books they bought to attest to their taste and refinement. Publishers responded to this market with machine-embossed designs that were often the work of well-respected artists. The cases they designed did more than name the author and the title of the book; they also gave an artistic impression of what the book was about. Publishers had invited the reading public to judge a book by its cover. Mass-produced books became collectibles.
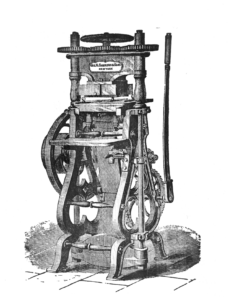
Engraving from a Sanborn sales catalog.
Sanborn advertised its No. 5 Embossing Press as very easy and convenient to operate by hand. The press could accommodate brass plates, or dies, large enough to be engraved with designs that could cover both the sides and spine of a case. The dies were clamped onto the press’s platen, the immovable downward-facing surface, which could be fitted to heat the die either by gas, hot irons, or steam. The platen for the No. 5 seen here was heated by gas (1).
To operate the embossing press, an operator placed the case face up on the press’s bed, which was the upward-moving surface not far below the platen. Pulling down the vertical lever on the right raised the bed to meet the platen, embossing the case under great pressure. This vertical lever was a Sanborn innovation (noted by British periodical The Bookseller in June, 1862, in its review of bookbinding equipment at the Great London Exposition (2)) which required less force to exert more pressure than the horizontal lever had done.
The No. 5 could be adjusted to the task. It could emboss cases measuring up to nineteen and a half inches from edge to edge. The depth of the impression to be made in the case could be regulated by turning the wheel at the top of the machine. With an eye to the future, Sanborn also offered the No. 5 as a power embosser, fitted to run on electricity with a flywheel that could convert it to manual use.
In 1855, Harper Bros. expected an operator on a machine similar to the Sanborn embosser to emboss sixteen cases a minute (3)
1) ABM’s Sanborn press was the gift of Michael Atha of Restoration Books Bindery and Fine Press in Logan, Utah.
2) “Mr. Sanborn, the American exhibitor, has, what appears to us to be, a very useful Arming Press, in which all the works are below and almost out of sight, while the action of the lever is downward instead of vertical.” The Bookseller, June 30, 1862.
3)For an illustrated description of the Harper Brothers’ steam-powered factory, see Jacob Abbott, The Harper Establishment, or How the Story Books Are Made, New York: Harper Bros., 1855. It can be found at https://archive.org/details/harperestablishm00abbo/page/n7/mode/2up.